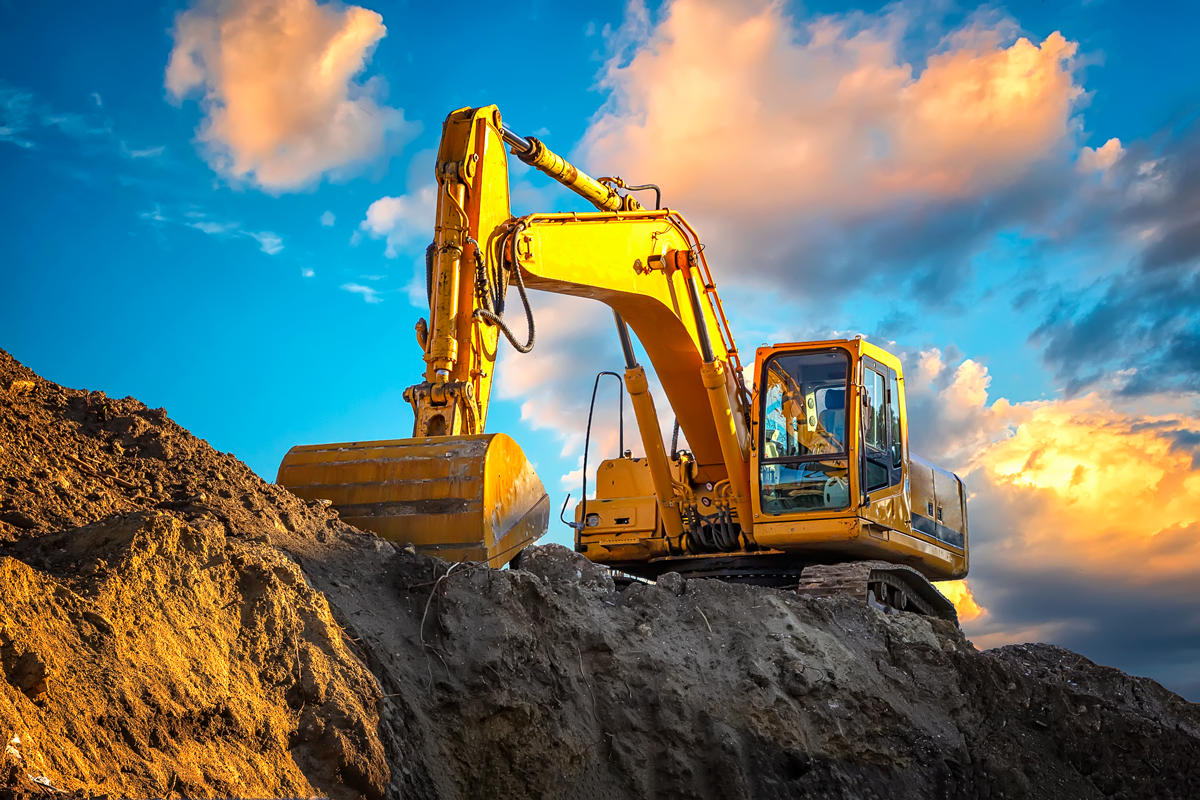
Construction projects rely on heavy equipment to stay on schedule, but downtime from repairs or delays in parts can lead to costly setbacks and inefficiency.
Construction projects are fast-paced and demanding, and equipment plays a critical role in keeping things on track. Whether it’s excavators, bulldozers, cranes, or aerial lifts, downtime can quickly turn a project into a costly and delayed endeavor. Unplanned repairs, mechanical failures, or even waiting for parts can bring work to a standstill, causing frustration and wasted resources.
Minimizing equipment downtime is essential for keeping your construction project on schedule and within budget. Here are a few strategies to reduce the likelihood of downtime and ensure your machines keep working efficiently.
The most effective way to minimize downtime is through proactive maintenance. Regular inspections, oil changes, and part replacements can catch potential problems before they develop into costly repairs. Establishing a preventative maintenance program for your equipment ensures that each machine gets the care it needs on a set schedule, reducing the likelihood of unexpected breakdowns.
Routine maintenance also helps improve the longevity of your equipment, ensuring that your machinery stays in service longer without requiring expensive, time-consuming repairs.
While it may be tempting to cut costs by purchasing cheaper equipment or using low-cost parts, this can lead to more frequent breakdowns and higher long-term costs. Invest in high-quality, durable equipment and parts that are designed to handle the demands of construction projects.
It’s important to use original parts and materials from trusted manufacturers, as these are more likely to meet safety standards and provide long-term reliability. Poor-quality parts can wear out quickly, leading to more repairs and extended downtime.
Sometimes, equipment downtime is a result of operator error or improper usage. Proper training is essential to ensure that your team knows how to safely operate and care for the machinery. Operators should be trained on routine maintenance tasks like checking fluid levels, inspecting hoses, and identifying any abnormal sounds or behaviors from the equipment.
When your team understands the nuances of your equipment and how to maintain it, they can identify potential issues early and reduce the risk of breakdowns.
Another way to minimize downtime is by keeping critical spare parts in stock. Having essential components—such as filters, belts, hoses, and hydraulic fluid—on hand can help you quickly address issues without having to wait for parts to be ordered. In case of a sudden malfunction, having a well-stocked inventory can get your equipment back to work faster.
Establishing relationships with reliable suppliers who can deliver parts quickly is also a key strategy in minimizing downtime during repairs.
In today’s digital age, many construction companies are using telematics and other monitoring systems to track equipment performance in real time. These technologies can alert you to issues like overheating engines, fuel inefficiency, or low oil levels before they result in major breakdowns.
By tracking performance data, you can schedule maintenance or repairs during planned downtime, preventing unexpected failures from disrupting work. This data also allows you to optimize your fleet’s usage, ensuring you’re getting the most out of your machinery.
Even with the best planning, equipment failure can still happen. That’s why it’s essential to have a contingency plan in place for when unexpected breakdowns occur. Whether it’s having backup equipment available or arranging for emergency repairs, being prepared for the unexpected will help you minimize downtime and keep your project on track.
A solid plan allows your team to react quickly and get the project back up and running as soon as possible, reducing the impact of any unforeseen issues.
Minimizing equipment downtime is a critical component of successful construction project management. Through regular maintenance, proper training, investing in quality equipment, and staying ahead with spare parts and technology, you can ensure your machinery keeps running smoothly. By staying proactive and prepared, you can reduce delays, avoid costly repairs, and keep your construction projects on time and within budget.
At Brown’s Heavy Equipment, we specialize in providing expert repairs, parts, and services that help reduce downtime for construction companies. Whether you need scheduled maintenance or emergency repairs, our experienced technicians are here to keep your equipment running at its best. Contact us today to learn how we can help your fleet stay operational and minimize downtime on your next project!